Revolutionizing Construction Efficiency: How Lean Practices Transform Project Delivery
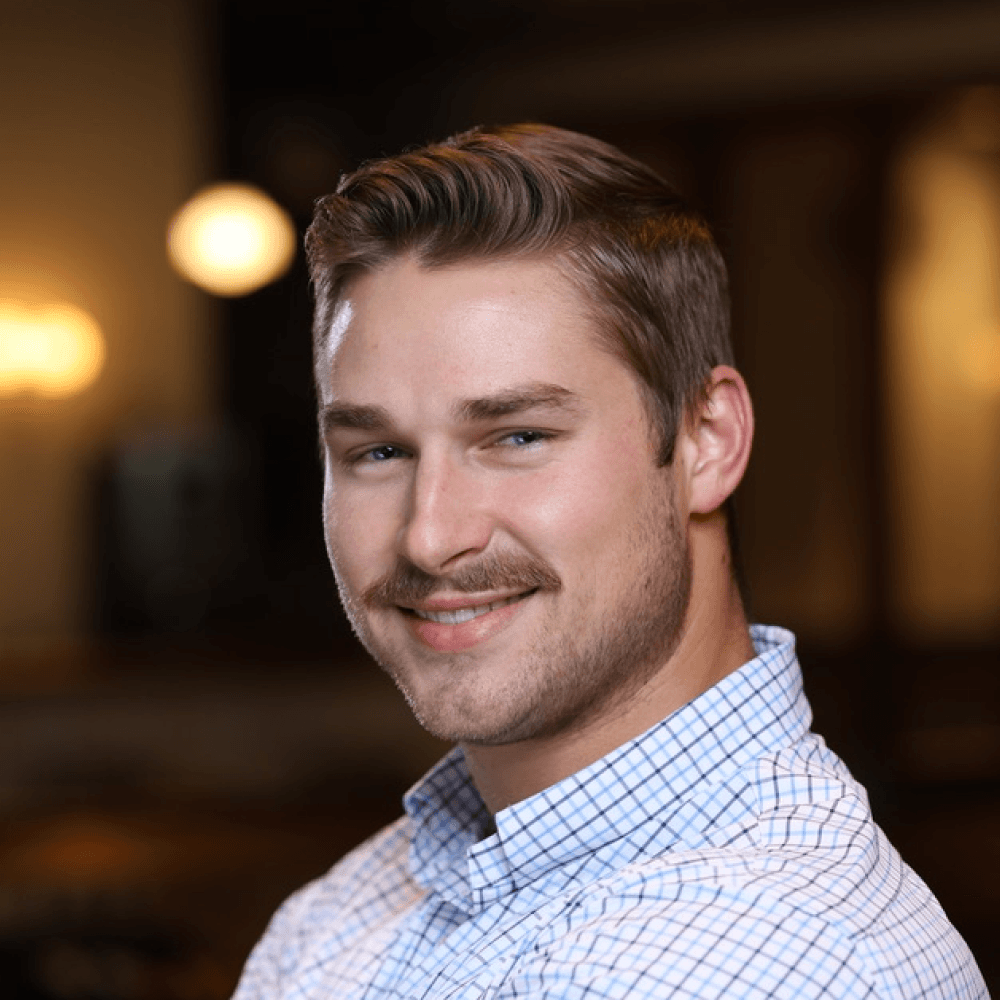
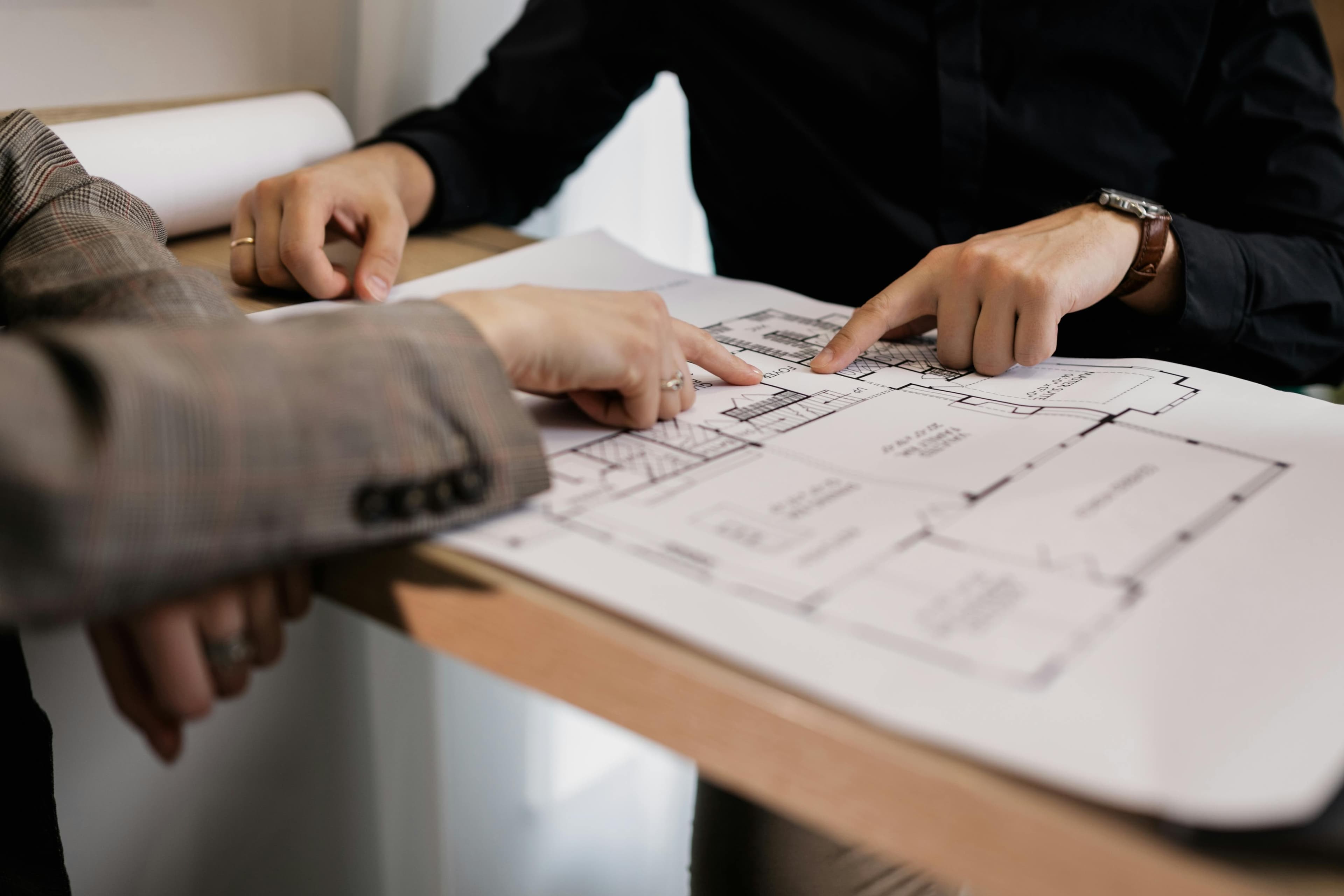
Discover how lean construction principles are revolutionizing project delivery, reducing waste, and improving outcomes in the construction industry.
Revolutionizing Construction Efficiency: How Lean Practices Transform Project Delivery
In an industry known for thin margins and high waste, lean construction offers a methodology that can fundamentally transform how projects are conceived, designed, and delivered. By applying principles first developed in manufacturing to the complex world of construction, companies are achieving remarkable improvements in productivity, quality, and client satisfaction. This comprehensive guide explores the core concepts of lean construction, its practical applications, and how it's reshaping the future of the industry.
The Evolution of Lean Construction
Lean construction emerged from the manufacturing sector's successful lean production systems, most notably Toyota's Production System developed in the 1950s. This approach revolutionized manufacturing by focusing on eliminating waste (muda), implementing continuous improvement (kaizen), and emphasizing respect for people. The translation of these concepts to construction began in earnest in the early 1990s.
The principle of lean in construction is primarily focused on eliminating waste in process activities to reduce cycle times, improve quality, and increase overall efficiency. In the lean context, waste encompasses all forms of overproduction, overprocessing, delays, excess inventory and motions, failures, and defects.
What makes lean construction distinct from traditional construction approaches is its emphasis on three key perspectives of production:
- Transformation - Converting inputs into outputs through resources, equipment, and workers
- Flow - Ensuring smooth movement of materials, information, and activities
- Value - Focusing on customer needs and expectations
Core Principles of Lean Construction
1. Maximize Value
At its foundation, lean construction begins with understanding what constitutes value from the client's perspective. This requires a clear definition of what the client truly needs and values, beyond simply meeting minimum specifications. The goal is to deliver maximum value while minimizing waste in all its forms.
2. Identify the Value Stream
Lean construction emphasizes mapping the entire construction process to identify areas of waste and inefficiency. By scrutinizing each step in the value stream, teams can pinpoint opportunities for improvement. This involves analyzing all activities - from design and procurement to construction and handover - to determine which add value and which don't.
3. Create Flow
Traditional construction processes often involve stop-start work patterns with significant waiting periods between activities. Achieving a smooth, continuous workflow is crucial in lean construction, involving the minimization of interruptions and bottlenecks to ensure tasks move seamlessly from one phase to another. This principle aims to eliminate the "hurry up and wait" syndrome common on many construction sites.
4. Establish Pull
In conventional construction, work is often "pushed" according to a predetermined schedule regardless of whether the next work area is ready. Unlike traditional push systems where work is assigned regardless of readiness, lean construction employs pull systems where tasks are only started when the preceding task is completed, reducing overproduction and excess labor. This approach ensures that resources are only applied when they can be effectively utilized.
5. Pursue Perfection
Lean construction is committed to continuous improvement through iterative feedback and learning. Teams regularly reflect on their processes and make adjustments to enhance efficiency and quality. This principle recognizes that perfection is never achieved but must be constantly pursued through ongoing refinement of processes.
Key Methodologies in Lean Construction
The Last Planner System®
The Last Planner System (LPS) is perhaps the most widely recognized and implemented lean construction tool. When implemented with diligence and consistency, projects using the Last Planner System see near-immediate improvements in workflow reliability, schedule performance, and worker morale. This collaborative planning approach brings together those who will actually perform the work to develop detailed, realistic schedules.
The system operates through several hierarchical planning levels:
- Master Scheduling - This high-level planning phase looks at what should happen and breaks down multi-year projects into 10-15 key milestones that focus on the start of critical activities like foundations, structural steel, and production drywall.
- Phase Planning - Teams collaboratively plan specific project phases, working backward from milestones to determine the optimal sequence of activities.
- Look-Ahead Planning - Teams identify and remove constraints for activities that will occur in the next 3-6 weeks.
- Weekly Work Planning - The team makes reliable commitments for the coming week based on prerequisites being in place.
- Daily Coordination - Brief daily meetings ensure the plan is on track and address any emerging issues.
- Learning - Metrics like Percent Plan Complete (PPC) are tracked and visualized on scoreboards where trade partners can see them, along with upcoming milestones, days left in the project, and commitments made/missed as part of a Lean dashboard system. This creates accountability and drives continuous improvement.
Target Value Delivery
Target Value Delivery (TVD) flips the traditional design-estimate-redesign cycle by establishing cost targets upfront and designing to meet them. This approach:
- Establishes a realistic budget early in the process
- Integrates cost considerations into design decisions
- Uses cross-functional teams to find innovative solutions
- Relies on continuous estimating rather than periodic cost checks
Integrated Project Delivery
Integrated Project Delivery (IPD) is a triparty contract that fosters collaboration by aligning the owner, design team, and construction team under a single agreement with shared financial targets, where all parties share in both profits and savings. This creates a powerful "skin in the game" dynamic that motivates everyone to improve outcomes.
While IPD isn't feasible for every project, its collaborative principles can be applied even within traditional contracting methods.
The Benefits of Lean Construction
The implementation of lean construction principles yields significant benefits across multiple dimensions:
1. Reduced Waste and Increased Efficiency
Lean construction cuts project time by up to 25% and costs by as much as 50% by maximizing value and minimizing waste across all phases of construction. This remarkable efficiency gain comes from eliminating the various forms of waste that plague traditional construction processes.
2. Improved Quality and Safety
By focusing on doing things right the first time and establishing standardized processes, lean construction significantly reduces defects and rework. The emphasis on planning and preparation also creates safer work environments with fewer accidents.
3. Enhanced Collaboration and Communication
Lean construction breaks down the traditional silos between design, engineering, and construction teams. The silos created around architects, designers, engineers, general contractors, trade contractors, and specialty providers have historically introduced significant waste into the delivery system along with a lack of trust that created systems of checks, double-checks, and over-specification. Lean practices address these problems through improved communication and collaboration.
4. Greater Customer Satisfaction
By focusing on value from the customer's perspective, lean projects are more likely to meet or exceed client expectations. This customer-centric approach ensures that resources are directed toward features and attributes that matter most to the client.
5. Reduced Administrative Burden
One often overlooked benefit of lean construction is its potential to dramatically reduce administrative overhead. One major obstacle to maximizing worker productivity is the completion of administrative tasks like manual daily reports, field notes, and photo uploads that reduce time available for project-specific work. Lean construction addresses this through streamlined processes and thoughtful technology integration.
Real-World Implementation Challenges
Despite its proven benefits, lean construction adoption faces several common challenges:
1. Resistance to Change
A major gap exists in the perception of industry inefficiency - while nearly two-thirds of contractors involved with the Lean Construction Institute rate the U.S. design and construction industry as inefficient, only 30% of the broader industry agree. Until this fundamental perception changes, the challenges associated with adopting lean may outweigh the benefits for many general contractors.
2. Lack of Expertise
The biggest challenge for many organizations is a lack of staff with sufficient lean expertise, reported by 64% of LCI respondents and the second biggest challenge for the broader industry. This expertise gap creates a significant barrier to effective implementation.
3. Short-Term Focus
The construction industry's project-based nature often creates pressure for immediate results, making it difficult to invest in processes that may take time to yield their full benefits. Lean construction requires a longer-term perspective focused on continuous improvement.
4. Fragmented Industry Structure
The highly fragmented nature of the construction industry, with numerous specialized subcontractors on each project, complicates the implementation of lean practices across the entire value chain.
Starting Your Lean Construction Journey
For organizations looking to implement lean construction practices, these steps provide a structured approach:
1. Educate Leadership
Begin with leadership education about lean principles and potential benefits. Without strong leadership commitment, lean initiatives are unlikely to succeed. Provide concrete examples of successful lean implementations and their measurable benefits.
2. Start Small
Rather than attempting a wholesale transformation, begin with pilot projects or specific processes where lean principles can be applied. The Last Planner System is often an excellent starting point as it provides a structured approach to planning and can deliver quick wins.
3. Focus on Culture
Respect for people is a fundamental pillar of lean construction, and many teams focus on particular lean methods or tools without starting with respect first, which can lead to short-term wins but no long-term gains. Creating a culture of continuous improvement and respect is essential for sustainable lean implementation.
4. Measure and Learn
Establish baseline measurements before implementing changes, then track progress using appropriate metrics. Regularly review results, celebrate successes, and learn from setbacks to continuously refine the approach.
5. Leverage Technology
While lean is fundamentally about processes and people, technology can be a powerful enabler. Modern construction management platforms that incorporate lean principles can help streamline workflows, improve visibility, and reduce administrative burden.
How Rethink Supports Lean Construction
Our platform is specifically designed to support lean construction principles by:
- Eliminating Administrative Waste - Our voice-assisted documentation allows field personnel to capture observations, daily logs, and issues without the time-consuming paperwork traditionally required.
- Enhancing Collaboration - Our communication tools break down silos between project participants and ensure that everyone has access to the information they need, when they need it.
- Supporting Last Planner Implementation - Our scheduling tools are built around lean principles, making it easier to implement and maintain pull planning and constraints management.
- Enabling Visual Management - Real-time dashboards provide visibility into project status, performance metrics, and potential issues, supporting the lean principle of making work visible.
- Facilitating Continuous Improvement - Our analytics capabilities help teams identify patterns, track improvement over time, and share lessons learned across projects.
Conclusion: The Future of Construction is Lean
As the construction industry faces increasing pressure to improve productivity, reduce costs, and enhance sustainability, lean principles offer a proven path forward. By focusing relentlessly on value creation and waste elimination, lean construction not only improves project outcomes but also addresses many of the systemic challenges facing the industry.
The journey toward lean construction is not without its challenges, but organizations that commit to this approach stand to gain significant competitive advantages. As more success stories emerge and expertise grows, lean construction is increasingly moving from a niche methodology to an industry standard.
For forward-thinking construction professionals, the question is no longer whether to adopt lean practices, but how quickly and effectively they can be implemented to transform their operations and deliver greater value to clients.