The Staggering Cost of Poor Productivity in Construction
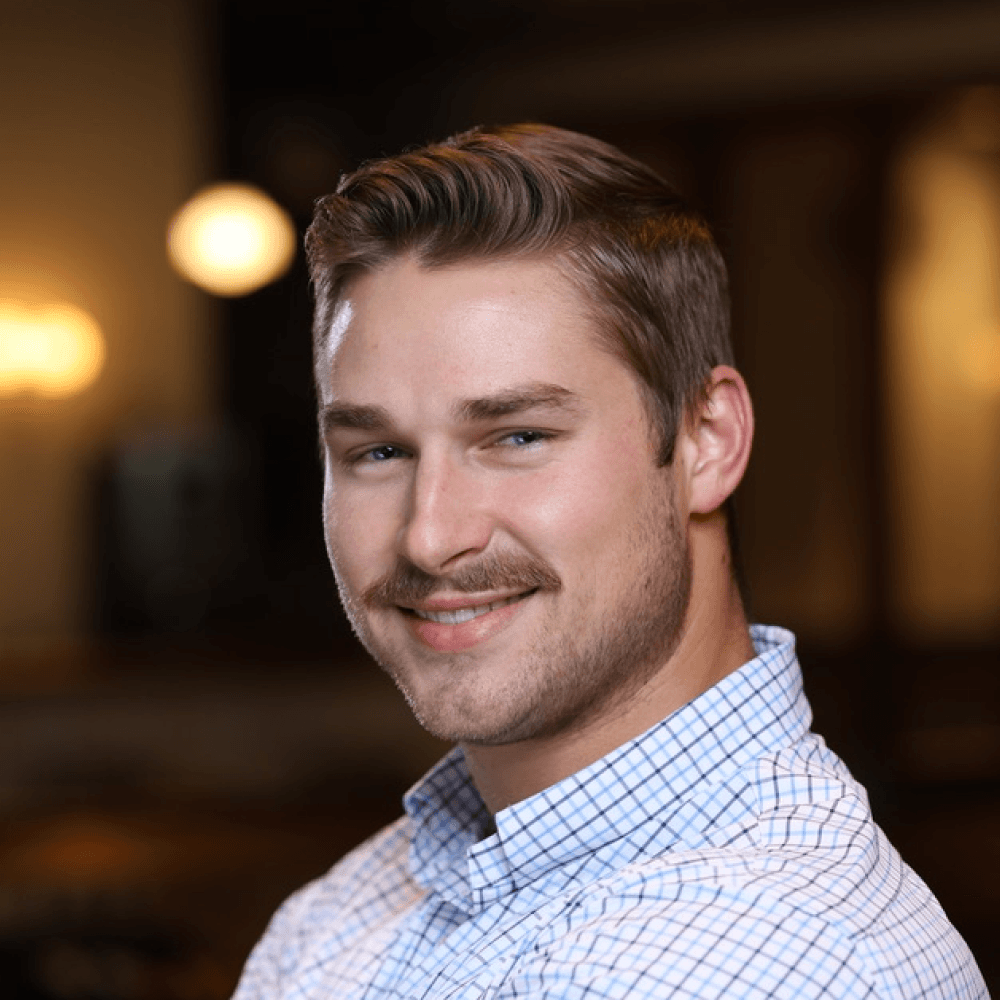
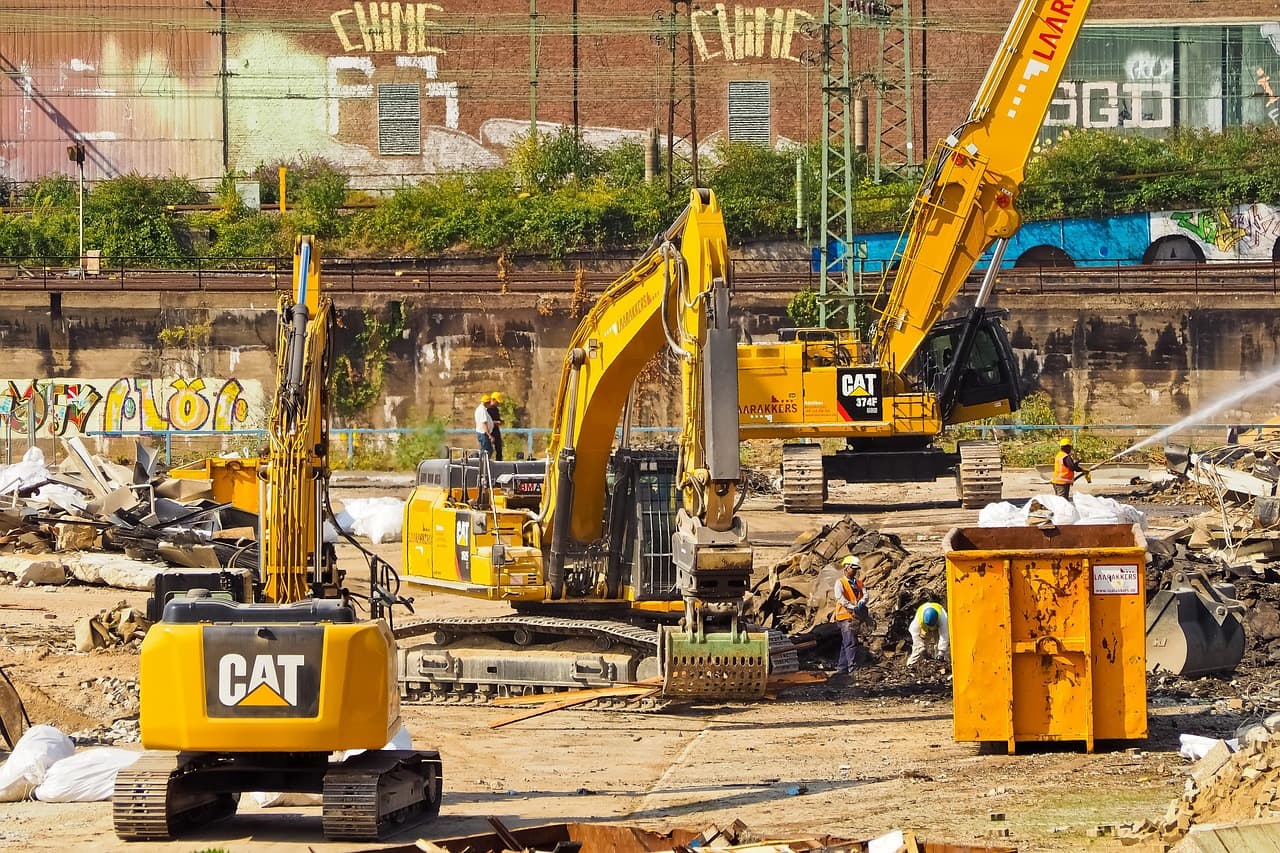
Explore the billions lost annually to construction productivity inefficiencies and discover how lean principles, technology adoption, and systematic planning can help companies transform their performance and profitability.
The Staggering Cost of Poor Productivity in Construction
In an industry struggling with paper-thin profit margins, the construction sector continues to hemorrhage billions of dollars annually due to productivity inefficiencies. Despite technological advances in other industries, construction productivity has remained stagnant or declined for decades, creating a significant economic burden for companies, clients, and the economy as a whole. Understanding the true cost of this productivity crisis is the first step toward implementing effective solutions.
The Productivity Crisis by the Numbers
The scale of construction's productivity problem is staggering. Of the nearly $900 billion in construction put in place by labor-intensive contractors in the United States in 2022, FMI research suggests contractors lost approximately $30 billion to $40 billion due to labor inefficiencies. This represents an enormous drain on an industry already operating with thin margins.
Even more concerning is the trend line. FMI's 2023 Labor Productivity Study confirms the well-documented trend of productivity decline, with only 23% of respondents claiming labor productivity improvements over the last 12-18 months, while 45% reported worsening productivity. This marks a significant deterioration from just a decade earlier, when 57% of those surveyed reported productivity improvements.
The historical context makes this decline even more alarming. Construction labor efficiency/productivity has decreased while all other non-farming labor efficiency has doubled or more since the 1960s. Currently, 70% of projects are over budget and delivered late. This divergence from other industries raises serious questions about the sector's fundamental approach to project delivery.
Where the Money Goes: Understanding Productivity Losses
The billions lost to poor productivity aren't simply disappearing — they're being consumed by specific inefficiencies that plague the construction process:
1. Labor Waste
Labor represents the largest variable cost in construction, making inefficiencies particularly costly. Contractors believe 11% to 15% of field labor costs are wasted or unproductive, and they conservatively estimate that 6% to 10% of labor spending ($15 billion to $25 billion) could be saved through better management practices.
These inefficiencies manifest in multiple ways:
- Waiting time due to poor coordination
- Rework caused by errors or changes
- Skilled workers performing unskilled tasks
- Excessive movement of people and materials around job sites
- Overstaffing to compensate for poor planning
2. Fragmented Project Delivery
The traditional construction process creates silos that impede productivity. The silos created around architects, designers, engineers, general contractors, trade contractors and specialty providers have introduced significant waste into the delivery system. A lack of trust has created systems of checks, double-checks and over-specification to cover legal ramifications.
This fragmentation results in:
- Communication breakdowns between design and construction teams
- Duplicate efforts as multiple parties check the same work
- Excessive documentation to protect against liability
- Delays in decision-making as issues are passed between parties
3. Poor Planning and Coordination
Without thorough planning, construction projects frequently encounter obstacles that could have been avoided. Projects that fall behind early rarely make miraculous recoveries. The discipline of in-depth, collaborative field and office planning before mobilization (pre-job planning) is one of the greatest influences on labor productivity.
Inadequate planning leads to:
- Material shortages or excesses
- Equipment idle time
- Trade stacking and interference
- Constant schedule adjustments and expediting
- Reactive rather than proactive problem-solving
4. Skilled Labor Shortages
The construction industry faces a growing crisis in finding and retaining skilled workers. As FMI's 2023 Talent Study revealed, 93% of firms can't find the workers they need, with the biggest gap in talent associated with field leadership.
This shortage affects productivity through:
- Less experienced workers requiring more supervision
- Increased training time for new hires
- Higher turnover disrupting team cohesion
- Projects operating with suboptimal crew sizes
- Field managers stretched too thin across multiple projects
5. Slow Technology Adoption
While other industries have embraced digital transformation, construction has been slower to adopt productivity-enhancing technologies. The construction industry is not exempt from the tendency to stick to old ways and resist change, though the many benefits of the lean approach are compelling more and more firms to take on the challenge.
This technological lag contributes to:
- Manual processes that could be automated
- Poor data collection and analysis
- Limited visibility into project performance
- Difficulty identifying and addressing inefficiencies
- Challenges in knowledge transfer between projects
The Business Impact: Beyond the Bottom Line
The cost of poor productivity extends far beyond direct financial losses. These inefficiencies create cascading effects throughout organizations and the industry:
1. Margin Erosion
In an industry with already thin margins, productivity losses can make the difference between profit and loss. At the individual contractor level, labor productivity deficits translate to project and enterprise margin erosion. With typical construction profit margins ranging from 2-8%, even small productivity improvements can significantly impact financial performance.
2. Reduced Competitiveness
Companies struggling with productivity find themselves at a disadvantage when bidding for projects. Those able to complete work more efficiently can offer more competitive pricing while maintaining profitability. Over time, this creates a widening gap between high-performing and struggling companies.
3. Project Delays and Budget Overruns
Poor productivity inevitably leads to schedule slippage and cost overruns. Currently, 70% of projects are over budget and delivered late. These failures damage contractor reputations, strain client relationships, and can trigger contractual penalties.
4. Safety Risks
When projects fall behind schedule, pressure mounts to accelerate work, often at the expense of safety protocols. LEAN principles mitigate potential safety hazards by providing a holistic view of the construction process, allowing team members to proactively address concerns, resulting in a safer working environment. Without these systematic approaches, safety often becomes secondary to schedule recovery.
5. Workforce Burnout
The stress of constantly fighting productivity issues takes a toll on workers at all levels. Field managers who shoulder the stress of on-site execution are particularly susceptible to burnout. FMI research found that executives expect 30% turnover for field managers over the next five years. This high turnover further exacerbates productivity challenges.
The Lean Solution: Transforming Construction Productivity
While the productivity crisis in construction is severe, proven solutions exist. Lean construction principles, adapted from manufacturing, offer a systematic approach to eliminating waste and maximizing value:
1. Focus on the Flow of Work
Lean construction views projects as flows of activities rather than just isolated tasks. LEAN principles eliminate waste and optimize processes by focusing on value-added activities and streamlining workflows, allowing personnel to complete tasks with fewer resources. This perspective helps identify and eliminate bottlenecks that impede productivity.
Key techniques include:
- Pull planning: Scheduling work based on when it's needed rather than pushing based on arbitrary dates
- Work flow visualization: Making the status of work visible to all project participants
- Constraint management: Proactively identifying and removing obstacles before they impact workflow
2. Early Stakeholder Integration
Breaking down traditional silos through early collaboration is essential to improving productivity. Lean construction results from applying a new form of production management that includes concurrent design, construction, and project control throughout the life cycle of the project from design to delivery.
Successful integration strategies include:
- Integrated project delivery (IPD): Contract structures that align incentives among all parties
- Co-location: Bringing key team members together in a shared workspace
- Design-assist: Involving builders in the design process to enhance constructability
- Target value design: Setting cost targets first, then designing to achieve them
3. Systematic Planning and Control
Detailed planning and continuous monitoring are fundamental to lean construction. FMI's data shows that the earlier field leaders are involved — and the better prepared they are before mobilization — the higher the profit margins.
Effective planning tools include:
- Last Planner System®: A collaborative approach to planning that involves those who will actually do the work
- Weekly work planning: Creating reliable commitments that align with the master schedule
- Percent Plan Complete (PPC) tracking: Measuring the reliability of weekly work plans
- Root cause analysis: Identifying why planned work wasn't completed
4. Continuous Improvement
Lean construction embraces the concept of ongoing refinement of processes. Continuous improvement—the belief that it is possible to continuously improve processes and eliminate waste—is the overall goal of lean philosophy. Opportunities for improvement are identified and acted upon during the project and applied to future projects.
Continuous improvement practices include:
- Plus/Delta reviews: Evaluating what went well and what could be improved
- Standard work: Documenting best practices for consistency
- Gemba walks: Observing work directly to identify improvement opportunities
- Knowledge transfer: Capturing lessons learned for application to future projects
5. Technology Enablement
While technology alone doesn't solve productivity issues, it can significantly enhance lean practices. Advanced Planning and Scheduling (APS) Software enables construction projects to have thorough visibility and insight into their operation and locate areas that need efficiency optimization.
Productivity-enhancing technologies include:
- Building Information Modeling (BIM): Digital representation of physical characteristics of a facility
- Mobile field tools: Applications that provide real-time access to information at the point of work
- Project management platforms: Centralized systems for document control and communication
- Data analytics: Tools that identify patterns and improvement opportunities in project data
The ROI of Lean Construction
The financial case for adopting lean construction practices is compelling. Companies that successfully implement lean principles consistently report significant benefits:
- Reduced project costs: Lean projects typically achieve 5-15% lower overall costs compared to traditional approaches
- Accelerated schedules: Schedule durations can be reduced by 10-30% through more efficient work flows
- Improved quality: Fewer defects and less rework result from systematic process improvement
- Enhanced safety performance: Proactive planning and hazard elimination reduce incident rates
- Higher employee satisfaction: More predictable work and less chaos improve worker experience
- Increased repeat business: Better project outcomes lead to stronger client relationships
How Rethink Helps Organizations Address Productivity Challenges
Our platform is specifically designed to address the productivity challenges facing the construction industry:
- Streamlined Communication: Our voice-assisted documentation eliminates the administrative burden of daily logs, RFIs, and other paperwork that traditionally consumes hours of productive time.
- Integrated Project Teams: Our collaborative tools break down silos between design, construction, and owner teams, fostering the early integration essential to lean construction.
- Visual Management: Interactive dashboards make project status transparent to all stakeholders, enabling quick identification and resolution of issues.
- Data-Driven Decisions: Analytics capabilities help teams identify productivity trends and improvement opportunities based on real project data.
- Knowledge Capture: Lessons learned are systematically documented and made available across projects, preventing the repetition of past mistakes.
Conclusion: Turning the Tide on Poor Productivity
The construction industry's productivity crisis represents both a challenge and an opportunity. The billions lost annually to inefficient practices indicate the magnitude of potential improvements. By addressing the root causes of poor productivity through lean construction principles, companies can transform their performance and profitability.
Forward-thinking organizations are already demonstrating that significant productivity gains are possible. These pioneers are not only improving their own bottom lines but also raising the bar for the entire industry. As more companies adopt lean methods, the sector as a whole will become more efficient, more sustainable, and more capable of meeting the world's growing construction needs.
The path forward is clear: embrace lean principles, invest in people and processes, leverage appropriate technology, and commit to continuous improvement. The companies that take these steps will not only stem the tide of productivity losses but position themselves for long-term success in an increasingly competitive market.